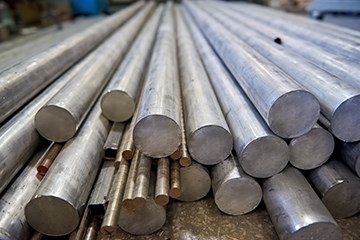
Rounds are sometimes mistakenly thought to be the easiest to straighten and are frequently the subject of customer complaints. However, symmetrical shapes are in fact the easiest to straighten.
To some extent, bar straightness is like the air we breathe – you only really think about it when it is polluted or not there at all.
In my nearly half a century of experience in manufacturing, most of which has been associated with the production and use of metal bars for machining, I have learned that bar straightness is a property that can be critical to a successful machining operation. The absence of adequate bar straightness can create a variety of issues, notably bar misfeeding problems, out-of-tolerance parts, excessive noise, premature machine wear and tool breakage. Those of you who own or manage a machine shop know this all too well.
Obviously, some machining processes are more sensitive to bar straightness issues than others. Those operations whose feedstock is a coiled rod or bar have mechanical design features that straighten or hold the material as part of their initial feed mechanism.
However, many operations require a high degree of bar straightness, especially when the material is to be presented to a machine by a bar feeder. For that sector of the market, the following is a brief review of the steps your bar supplier can take to ensure positive results. This discussion applies equally to all materials, including aluminum, brass, bronze and steel. Plus, it arms you with questions you can pose to your material supplier if straightness issues arise.
There are basically three types or configurations of straight barstock used as raw material for making machined parts: round stock; standard and symmetrical shapes (hexagons, octagons, squares); nonsymmetrical special shapes (double D, teardrop, key, twin lobe). Each type requires a different approach in its manufacture to ensure adequate straightness for the machining customer.
Opportunities to control (or ruin) bar straightness exist at eight stages of manufacture and delivery:
- Original hot working process (rolling or extrusion)
- Cold drawing process
- Final finishing (or straightening)
- Collecting and bundling
- Bundle handling and storage
- Shipping
- Unloading and storage at customer’s facility
- Loading bars into the customer’s machining process
Simply having proper standard operating procedures in place to ensure the bars are consistent right out of the drawing die is the key to supplying straight round stock, particularly cold drawn material. Subsequent “straightening” operations on rounds control internal stresses rather than absolute straightness. For example, leaded alloys can increase in diameter after aggressive straightening in two-roll operations (for example, on Medart or Mecco equipment). Control of such internal stresses can also be a deal breaker in nonleaded materials when the stock is machined asymmetrically – as when machining automobile steering racks, where one side of a round bar is selectively removed, potentially exposing the internal stresses that can result in bent finished parts if the effect of such stresses is not well understood and controlled by the bar supplier.
Rounds are sometimes mistakenly thought to be the easiest to straighten and are frequently the subject of customer complaints. However, symmetrical shapes are in fact the easiest to straighten. The bars must exit the cold finishing die straight. This simple notion requires a thorough understanding of the drawing operation by the bar supplier and the “management will” to develop proper techniques and control the process meticulously.
Nonsymmetrical shapes can be a challenge, but the key to providing a straight bar for the customer is manufacturing consistency. In many cases, the extrusion or the drawing operations have developed a technique to produce a slight but consistent bow, which when presented to the final straightening operation gives the opportunity to exert a consistent corrective pressure resulting in a straight bar.
Operations that focus on aggressive straightening only afterward often fail to appreciate the extent to which the product straightness can be controlled in extrusion or drawing. Control of straightness after the manufacturing operation is fundamentally about avoiding postproduction damage. Careful design and operation of bar handling, bundling, packaging, transportation, loading, unloading and storage often simply using basic common sense will go a long way toward ensuring that the product maintains its straightness right up to the point when the machine tool engages the bar in the customer’s facility.
About the Author
Roger Bassett is a retired company president and university professor who has enjoyed a more than 40-year career in the metals industry. He is currently assisting Franconia Industries and Diehl Brass Solutions with their business development. Bassett has served the Precision Machined Products Association through the years, holding many leadership positions and speaking at local and national meetings. Contact: 586-212-5122 or bassett@tm.net.
Related Content
Replace Repetitive Measurement With DIY Robotic Automation
After minimal training, a shop can learn how to use this robotic inspection system configured for a shopfloor application to supersede repetitive, time-consuming, high-mix gaging processes. It can then be redeployed for another application somewhere else in the facility.
Read MoreChuck Jaws Achieve 77% Weight Reduction Through 3D Printing
Alpha Precision Group (APG) has developed an innovative workholding design for faster spindle speeds through sinter-based additive manufacturing.
Read MorePursuit of Parts Collector Spearheads New Enterprise
While searching for a small parts accumulator for Swiss-type lathes, this machine shop CEO not only found what he was looking for but also discovered how to become a distributor for the unique product.
Read MoreHigh-Volume Machine Shop Automates Secondary Ops
An Ohio contract shop added a compact, self-loading CNC lathe to perform unattended secondary ops on a part for a key customer rather than running it on a manually loaded chucker.
Read MoreRead Next
Craftsman's Cribsheet No. 78: Straightness of Cold Finished Steel Bars
The straightness of cold finished steel bars, and all other barstock for our machines, is of critical importance.
Read MoreBar Feed Considerations For High-Speed, Lights-Out Machining
There are design elements incorporated into today’s 12-foot, magazine-load bar feeders that make them more useful for high-speed and untended operation. This article looks at some aspects to consider before purchasing a 12-foot bar feeder.
Read MoreApproach PMTS 2025 With a ‘Process’ Mindset
High-volume machining operations are more apt to think about the entire process of producing parts beyond the machine tools themselves. All such technology is presented at the 2025 edition of the Precision Machining Technology Show.
Read More